This website uses cookies so that we can provide you with the best user experience possible. Cookie information is stored in your browser and performs functions such as recognising you when you return to our website and helping our team to understand which sections of the website you find most interesting and useful.
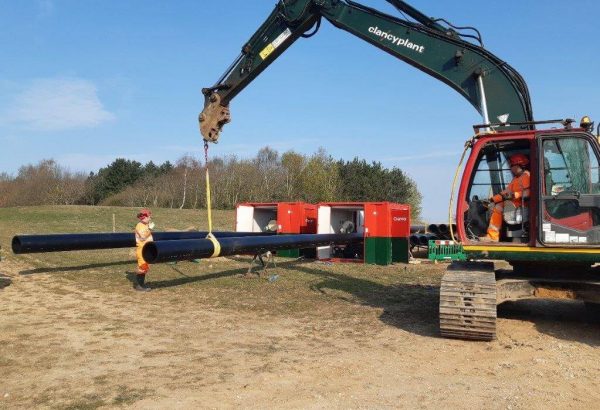
Case Study
Oasthouse – Crown Point Low Carbon
17,560
Hours
Zero
Accidents

Background
The UK imports more than 80% of its tomatoes, 75% of cucumbers, and 90% of its peppers, some from European countries facing water shortages. Whereas free movement of people and goods was once easy, challenges of Brexit and COVID-19 have raised potential concerns about the UK’s ability to sustainably fulfil its need for fresh produce. The low carbon farming initiative aims to make the UK increasingly self-sufficient in these items through a world-first renewable heating system, using waste energy from a local Water Recycling Centre (WRC) to heat a greenhouse development at Crown Point the size of 26 football pitches.
The greenhouses, being a world-first in their use of renewable energy, have positioned the UK as leading the way in a low carbon solution to growing sustainably, and will pave the way for similar projects.
Mark Dykes
Director - Stepp Associates
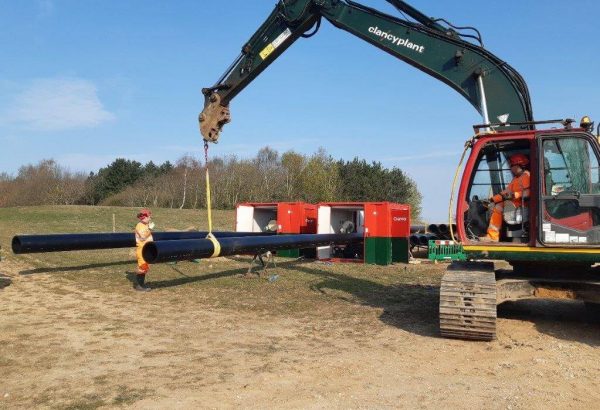
Solution
As a specialist pipeline contractor, Clancy were appointed to deliver the design, supply, installation, commissioning and testing of multi-utility works to connect the heat source (warm water from Anglian Water Services’ nearby Whitlingham WRC) and heat pumps to the greenhouse. More than 5km of underground pipeline was installed, including 2.6km of dual 560mm PE Heat Transfer Fluid (HTF) pipework, 2.4km of 33kV electric cable trenches and 170m of 180mm intermediate pressure gas main.
Benefit
Clancy’s long standing and established relationship with Anglian Water was invaluable to the project. Clancy provided a central role at design meetings, suggesting and implementing innovative engineering solutions on several aspects of the design. For example, using trenchless techniques (i.e. horizontal directional drilling) to help avoid rivers and protected vole habitats, and using caisson shaft techniques for wet well construction to reduce construction cost and duration, increasing sustainability and decreasing cost. Our team acted as Principal Contractor and this complex, multi-faceted project achieved an exceptional safety record, with zero accidents recorded over 17,560 working hours.